To stitch together how Knightsbridge makes its contract furniture, editor Hamish Kilburn travels up to Bradford in West Yorkshire to step inside the modern factory that chooses to do things the traditional way…
Priding itself on being 100 per cent British-made is something that has become somewhat of a unique selling point for contract furniture company Knightsbridge.
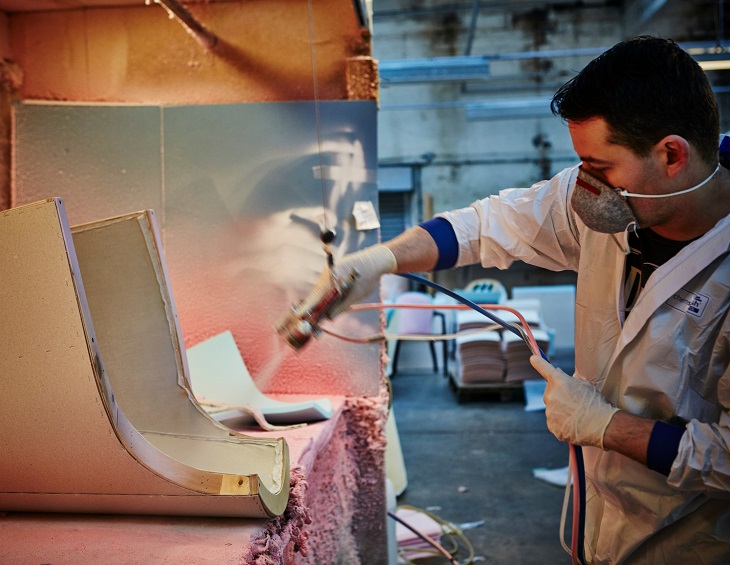
Giving ‘in-house’ a whole new meaning, every item that has a Knightsbridge logo on it was conceptualised, sketched, prototyped and produced in the hearty West Yorkshire town of Bradford – and has been for 80 years.
In an average week, around 700 items of furniture are made in the Victorian factory – and all pieces start as nothing more than a stacked load of timber or Birch plywood, which is imported from Russia and Europe. While many factories internationally have chosen to use automated machinery to carve their frames, Knightsbridge is among the minority that still, to this day, cuts its materials by the hands of skilled workers. “Many of our employees come through the apprenticeship scheme, which is something we are very proud of,” said Craig Weston, Operations Manager at Knightsbridge. “Because everything at Knightsbridge is handmade and hand-cut, the role in the factory therefore requires a very specific set of skills, which isn’t easy to teach just anyone.”
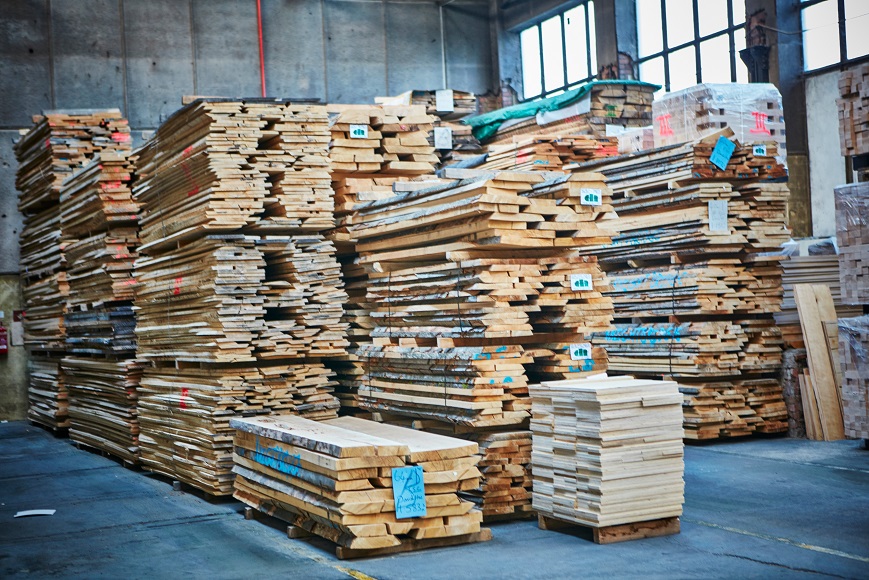
Image credit: Knightsbridge Furniture
As we walk from process to process, I notice that an arm of a chair starting to take form. “This is one of the most difficult pieces we make,” says Weston who points to the worker on the cutter who is meticulously carving out detailed incisions. “As a strategy, we ensure that we always have a higher stock of the items that are more complex to produce.” With high demand for Knightsbridge products and limited facilities, this is a resourceful method that reduces the possibility of delays in the manufacturing process.
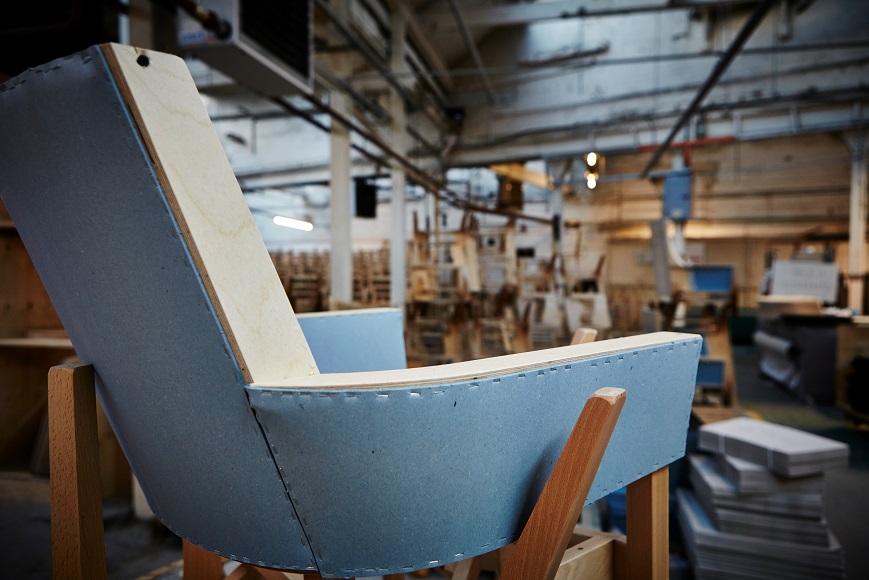
Image credit: Knightsbridge Furniture
Once each frame is cut, sanded, assembled, tinted, polished and dried, it is then ready for the upholstery process. On average, it takes the team at Knightsbridge approximately one hour to upholster a typical sofa. As the demand in hotel interior design renovations increases, the company also offers a reupholstery service whereby it will reupholster any piece of furniture (even if it’s not a Knightsbridge product). The cluster of seamstresses working is impressive and the decision to keep a cap on fabric stock is reassuring. “To reduce waste and save space, we only stock as much material as we need in this area,” Weston explains. “What’s more, although we have colour and fabric options, we will match any colour the client wants.”
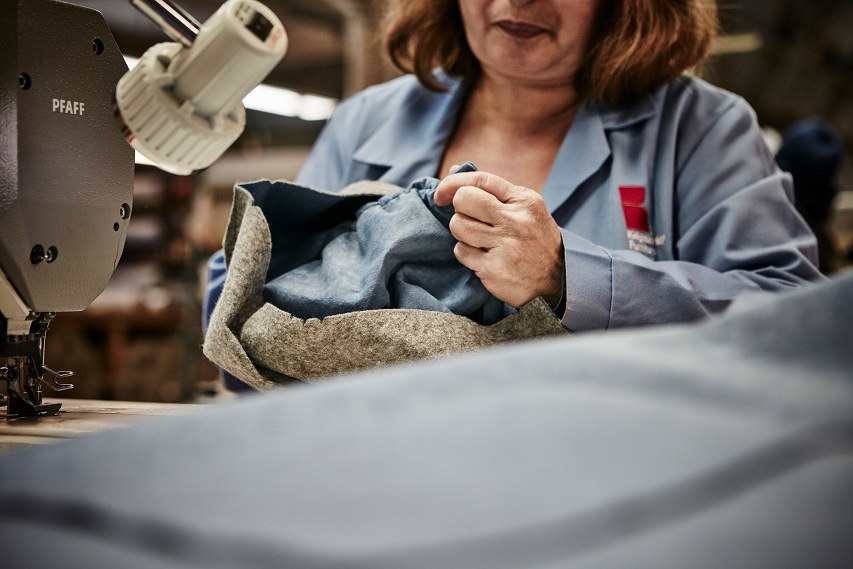
Image credit: Knightsbridge Furniture
Elsewhere in the factory, away from the main production line, is the design and development team. Led by Director Jason Brown, who lives and breathes by the ethos that you can’t turn down the volume on creativity, the soul of the factory is my home-from-from during my visit. “I have every furniture designers’ dream job, right?” laughs Brown. “It’s such a privilege being able to have all the tools, kit and skills to be able to prototype products in-house.” Brown is a man after my own heart who seems to wear many hats in his role. “The most obvious element to my role is that I sketch and design the future collections,” he explains. “But what most people perhaps don’t know is that my team, which is magic by the way, also have to provide the factory workers with all the technical drawings when we start producing a new product. As you can imagine, there is no margin for error in this department. We are always looking for new ways to be innovative, while being mindful of time, quality and cost for the overall business.” For Brown, like all great designers, thinking creatively and thinking commercially are difficult plates to spin at the same time. “It’s a challenge, but that’s why I love it,” he adds.
Despite Knightsbridge having the ultimate in-house design dream team, led by a visionary who clearly leads within the pack, the company is also proud to work with outside influences when designing future products. The latest collaborations to come out the factory include the likes of John Coleman, Sean Dare, Jim Hamilton and David Fox.
Knightsbridge is a modern company like no other. Proud of its heritage and confident to push boundaries, it seems as if this British-born company has all the materials, workforce and ideas – all stored under one roof – to lead the contract furniture market into another 80 successful years of business.