Inside the factory: behind the scenes with Porta Romana
Earlier this year, Editor Sophie Harper made her way to sunny Surrey to spend some time at Porta Romana headquarters – to find out more about the British lighting and furniture manufacturer and test her skills for gold-leaf application…
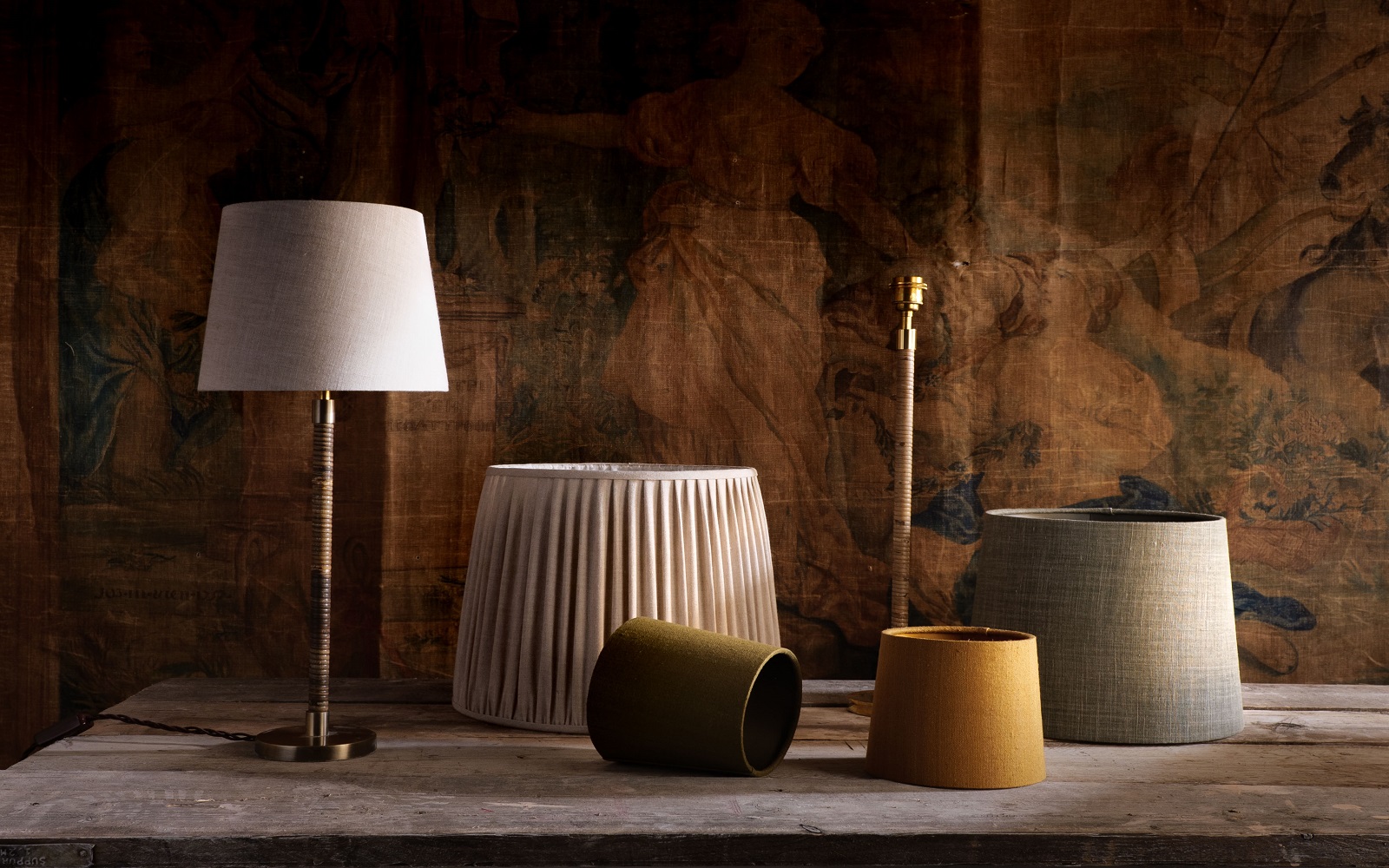
Arriving at Porta Romana HQ, it’s easy to see that this is a close-knit business with family values and pride at its core. A small group of us were welcomed into the fold on the day I visited, where we were introduced to the team and given an overview of the brand and its beginnings.
People commonly mistake Porta Romana for an Italian brand, but actually the business was founded by Andrew and Sarah Hills in 1988 – a British couple who adored their trips to Florence and were inspired by the labyrinth of streets around Via del Campuccio, filled with artisan workshops and little ateliers.
From a small workshop in the UK, the couple came up with ideas, sketches, and their first lighting products. Nearly four decades on and the ideas are still flowing, but on a much grander scale now with the brand’s iconic lighting and furniture adorning the likes of the Royal Academy of Arts in London to countless homes, galleries, and hotels all over the world.
Touring Porta Romana’s huge facility, we were led through the different departments – from lampshade building and fabric selection, to casting and testing – where we were met by skilled specialists to talk us through each process.
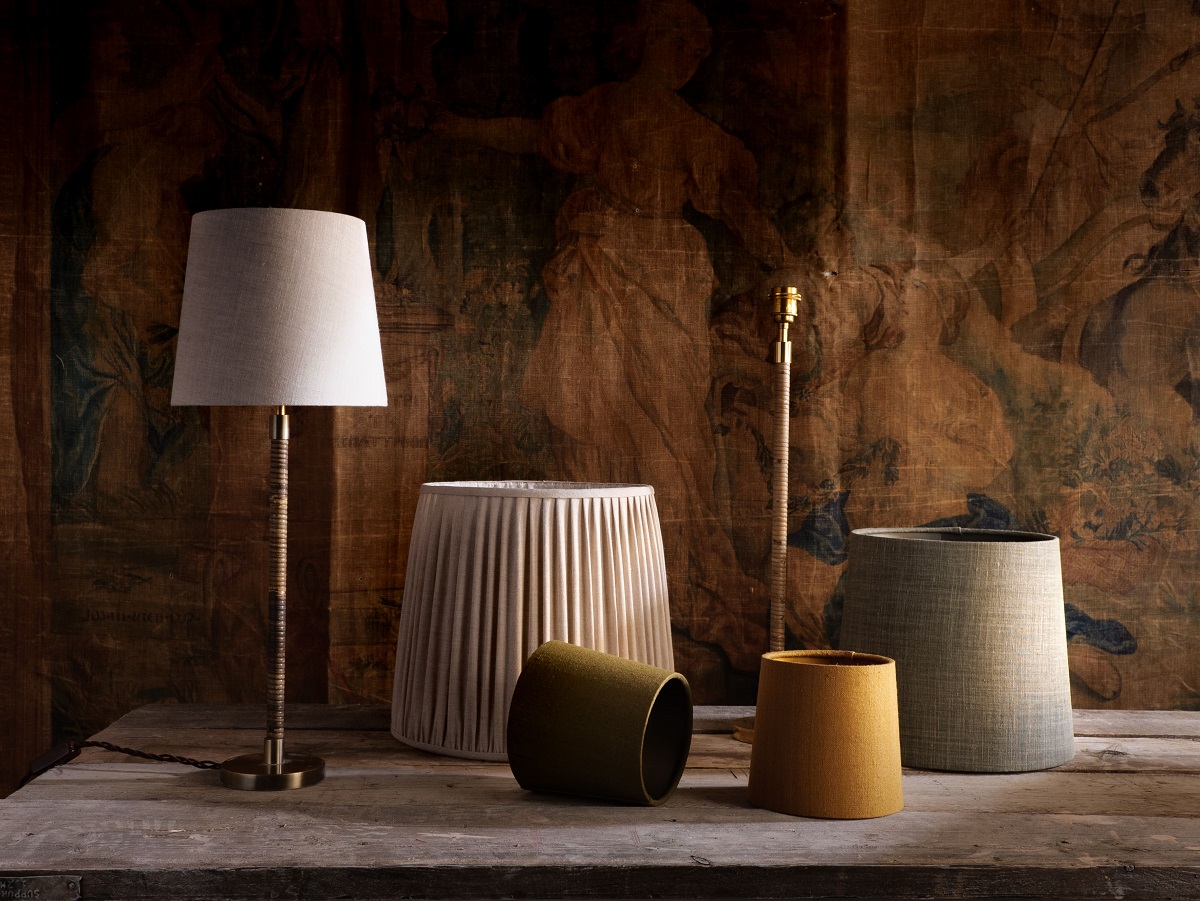
Image credit: Porta Romana
Telling us all about the numerous materials, trims, shapes, and sizes of different lampshades, Frannie – Porta Romana’s Lampshade Studio Manager and Green Team Ambassador – tells us how a multitude of combinations can be selected to create unique and bespoke lampshades to perfectly suit the bases they are paired with.
The group stared at the rolls upon rolls of fabric and large cutting tables surrounded by a plethora of vibrantly patterned and trimmed shades awaiting quality control checks.
Each piece of fabric is hand cut and the shade assembled by the team with acute attention to detail to ensure the brand’s high standards are met every time. Frannie tells us clients can even select and provide their own fabrics so long as they meet health and safety regulations – offering up even more scope for that one-of-a-kind design.
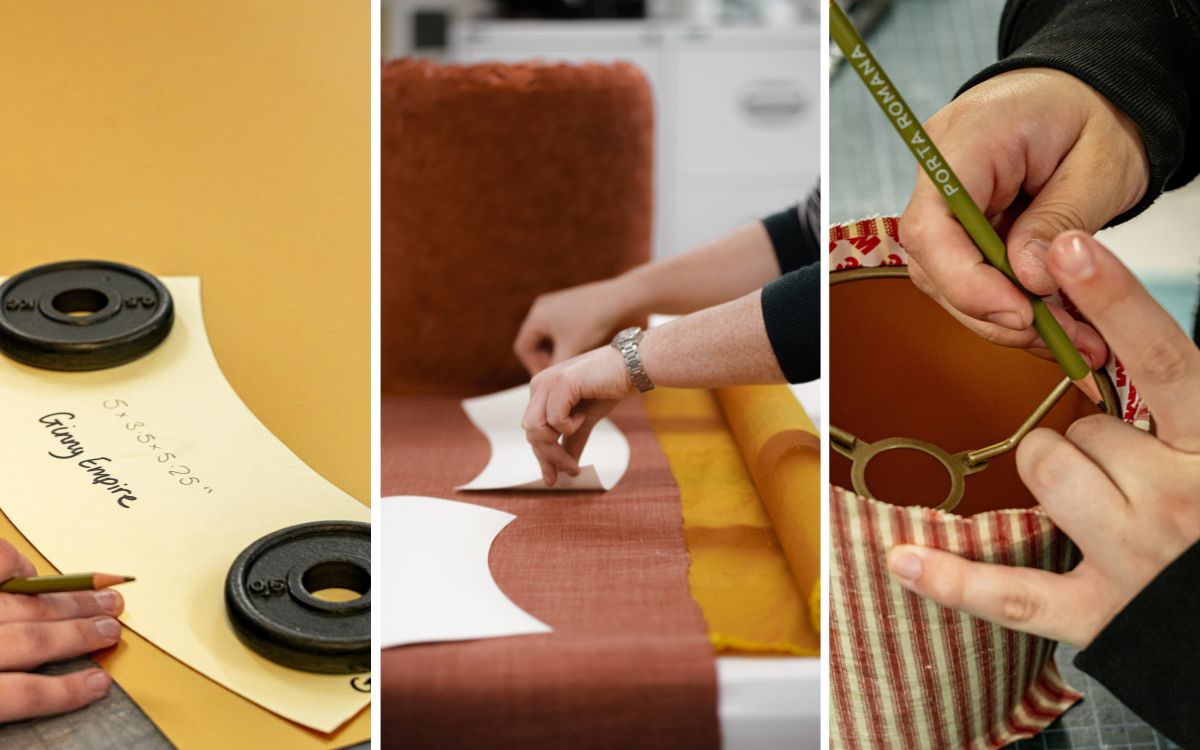
Image credit: Porta Romana
As one of the Green Team Ambassadors for the company, Frannie also tells us how every piece of waste is assessed – from fabric to gold leaf – to decide whether it can be reused or recycled.
Responsible design and striving to be more sustainable is serious business for Porta Romana. The company has invested a lot of time and effort into becoming as ‘green’ as possible, whilst recognising there is always more room to improve.
Porta Romana has invested in a number of initiatives, from bringing its lampshade studio in-house four years ago (saving 32,500 miles in transportation) and reducing landfill waste by 80% with its recycling scheme, to using biodegradable and recyclable materials, scaling back on packaging, and reducing energy consumption by 75% from 2016.
The business has also partnered up with Tala, the specialist LED bulb makers, to create its own lightbulbs with a lifespan of around 30,000 hours, which are included with every lighting product Porta Romana makes.
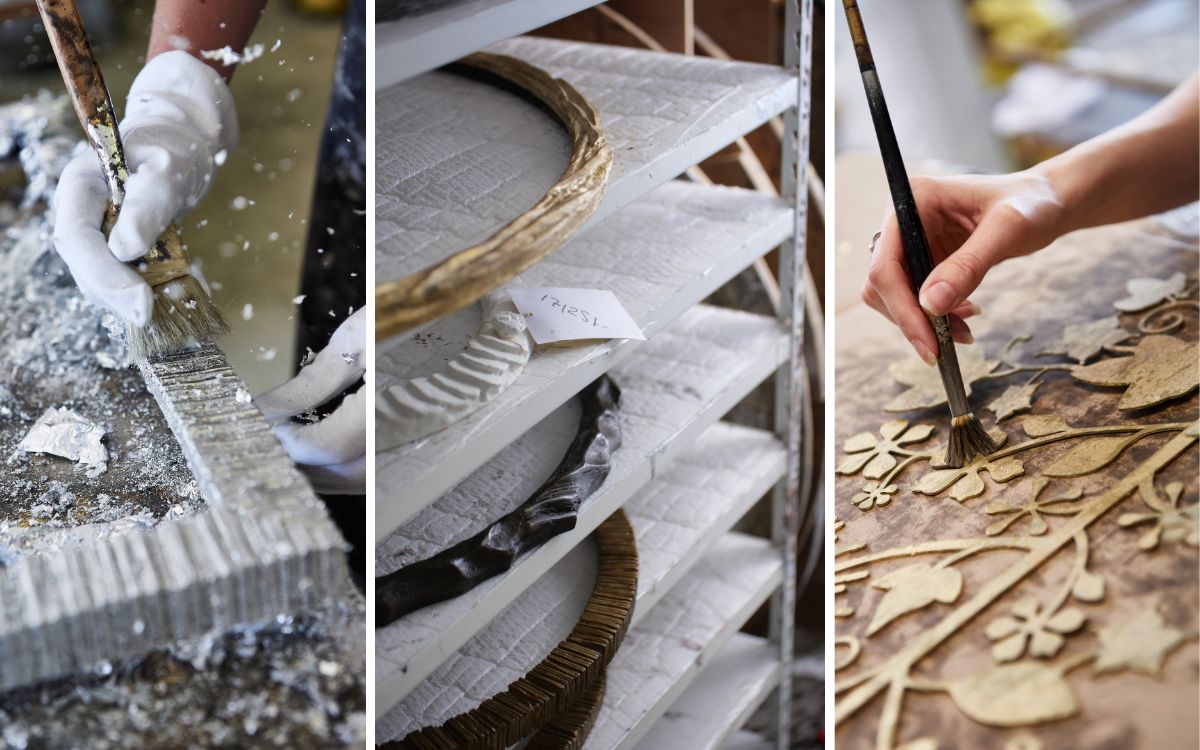
Image credit: Porta Romana
In fact, collaboration comes as second nature to Porta Romana… during our tour we were told of the close working relationships the company has with some of the UK’s finest craftspeople to help bring its unique designs to life. We learned how the brand’s well-known Perez lamp is hand-blown by local artist, Adam Aaronson, who uses traditional glassblowing methods to shape and form its unusual design.
After then talking to the furniture and packaging department and getting a glimpse of some of the latest collections, we headed to the painting studio where we got to see the ‘recipe book’ for all the tried and tested painted and patinated finishes. Like a creative art studio, there were pots of brushes lining the workstations, half painted sculptural forms, paper floral arrangements, and a very happy looking workforce of artists with rolled-up sleeves concentrating of all sorts of different projects.
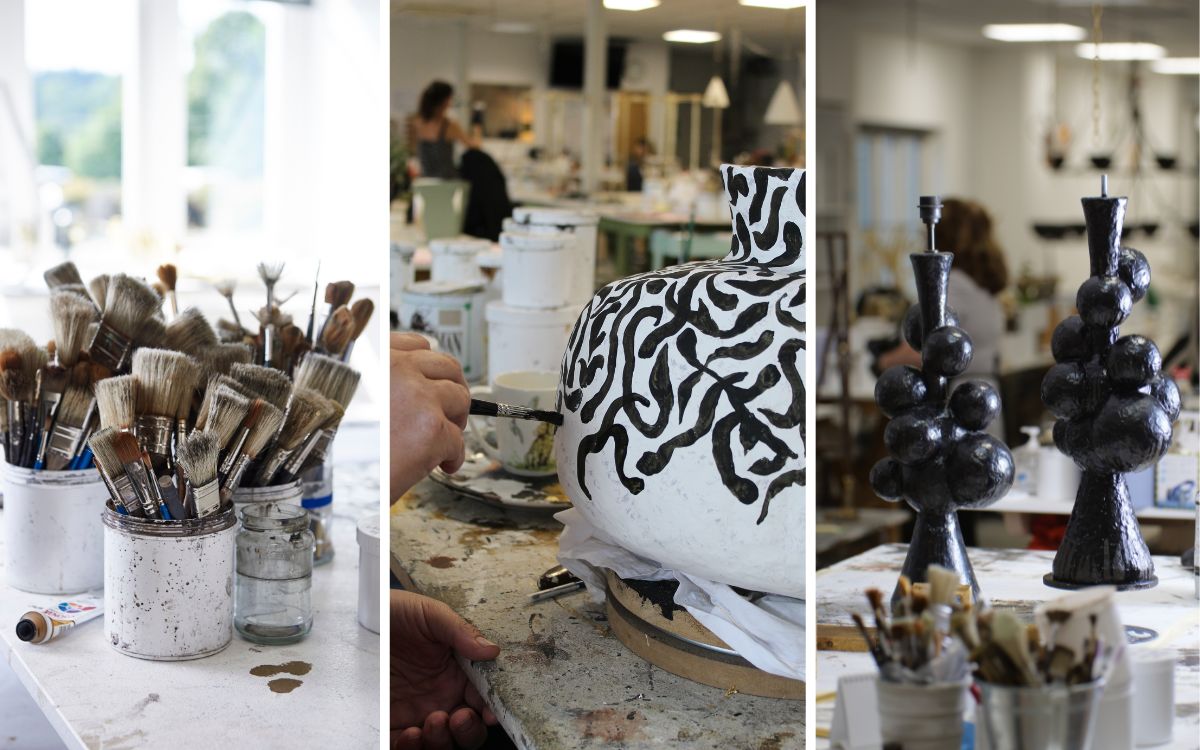
Image credit: Porta Romana
We were introduced to in-house artist, Kimberley, who told us we’d be creating our very own Porta Romana keepsake to take home with us! Already excited at the thought of getting crafty, I was even more delighted when we were each handed sheets of gold leaf. Kimberly talked us through the process of applying adhesive and then gold leaf to decorative pears, which we could keep as Christmas tree decorations.
At varying levels of competency, we wrapped and brushed the gold leaf to the pears before allowing it to bond. We then learned the proper Porta Romana technique for stippling to create the brand’s signature patina effect, which has been carefully developed by the team over the years. And I’m glad to say although I won’t be giving up the day job any time soon, I do have a passably pleasant looking decoration, which will of course be taking pride of place on my tree this Christmas!
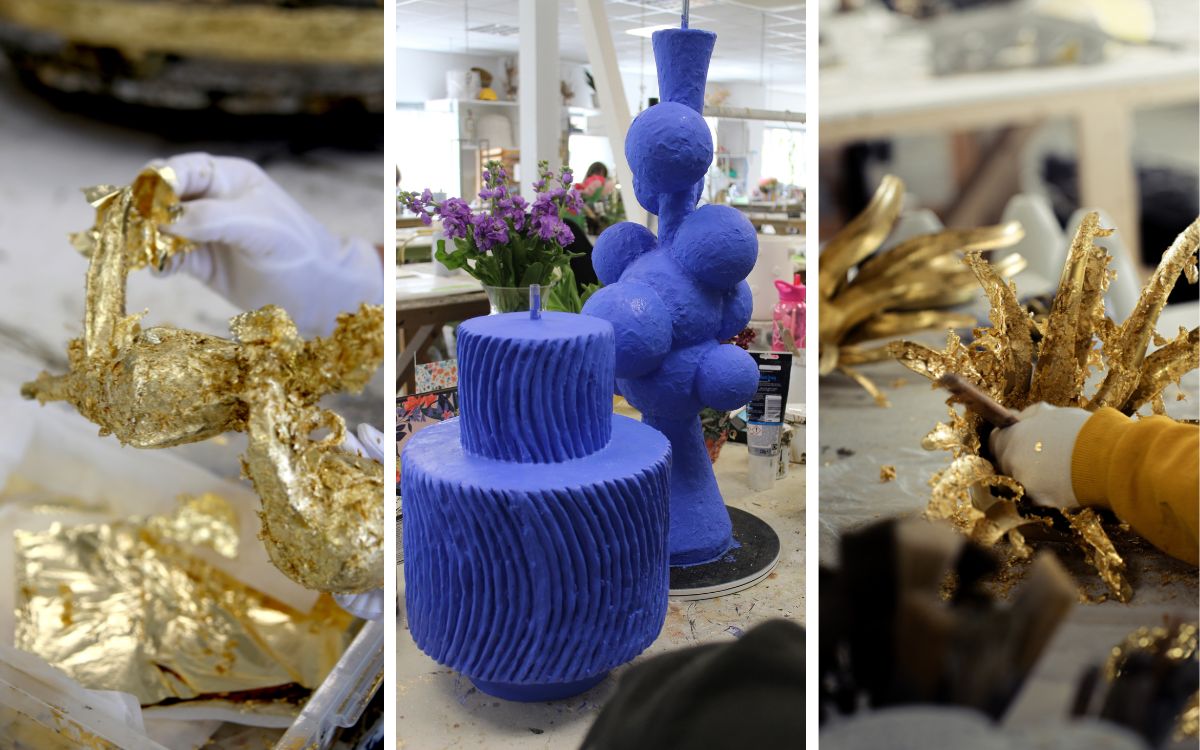
Image credit: Porta Romana
A fun and informative workshop, it certainly gave me a newfound respect for the skill and devotion of the entire team to create these beautiful products with such care and attention to detail. Each Porta Romana product is handcrafted, whether it’s selected from a collection or a bespoke design, every single item is made to order, which is an incredible feat of craftsmanship, and should be celebrated for keeping alive traditional skills and the magic of making.
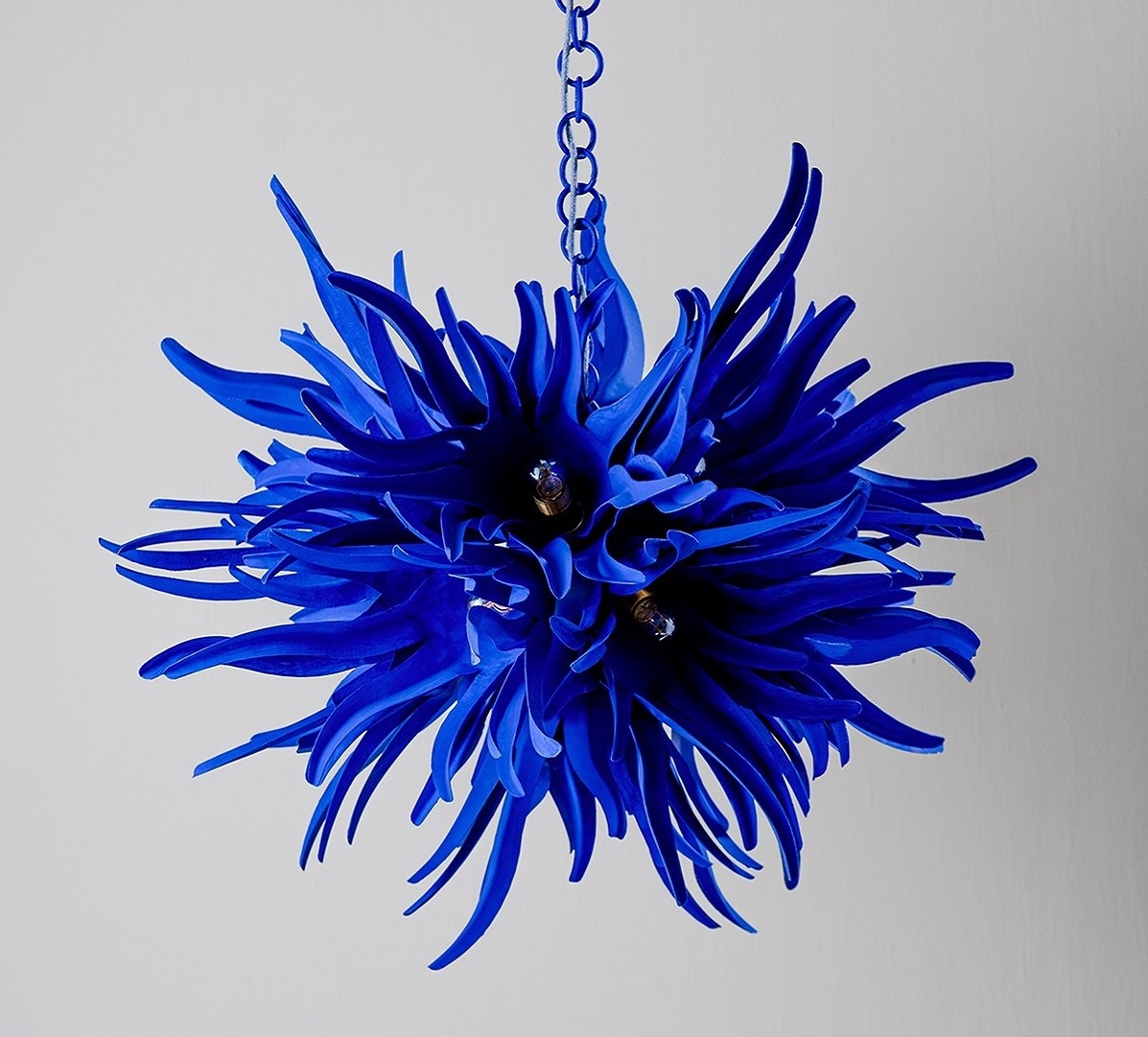
Image credit: Porta Romana
Porta Romana’s Urchin Chandelier was selected by The Brit List Awards 2024 judges as winner of Best in British Product Design for its impressive balance of modern technology and traditional craftsmanship. The judges commented: “The design is bold and visually striking, with each element meticulously handcrafted to create a unique piece. The chandelier’s production process includes traditional techniques such as hand-forming and painting. This thoughtful combination of innovative design and skilled craftsmanship makes it a standout product in British design.”
Read more about The Brit List Awards and our 2024 Award Winners.
Main image credit: Porta Romana