Editor Hamish Kilburn was given a sneak-peek preview of House of Rohl’s new RIBA-approved CPD course for Perrin & Rowe. Inside the bathroom brand’s Wolverhampton factory, designers and architects will soon be able to learn all stages of the manufacturing process, which starts with grains of sand…

Watching, hearing (even smelling) the 25kg brass ingots melt before being hand-poured into sand-casted moulds is a powerful experience. It is truly multi-sensory and, yes, it requires ear defenders.
Although casters can only create one fixture at a time, I’m surprised how quick the casting takes – it is, I’m told, the ame method used to make F1 components. The cooling is almost instant – blink and you will miss it. The seamless movement of lock, pour, tilt, open and cool has become ingrained in the minds of the skilled casters here inside Perrin & Rowe’s Wolverhampton factory.
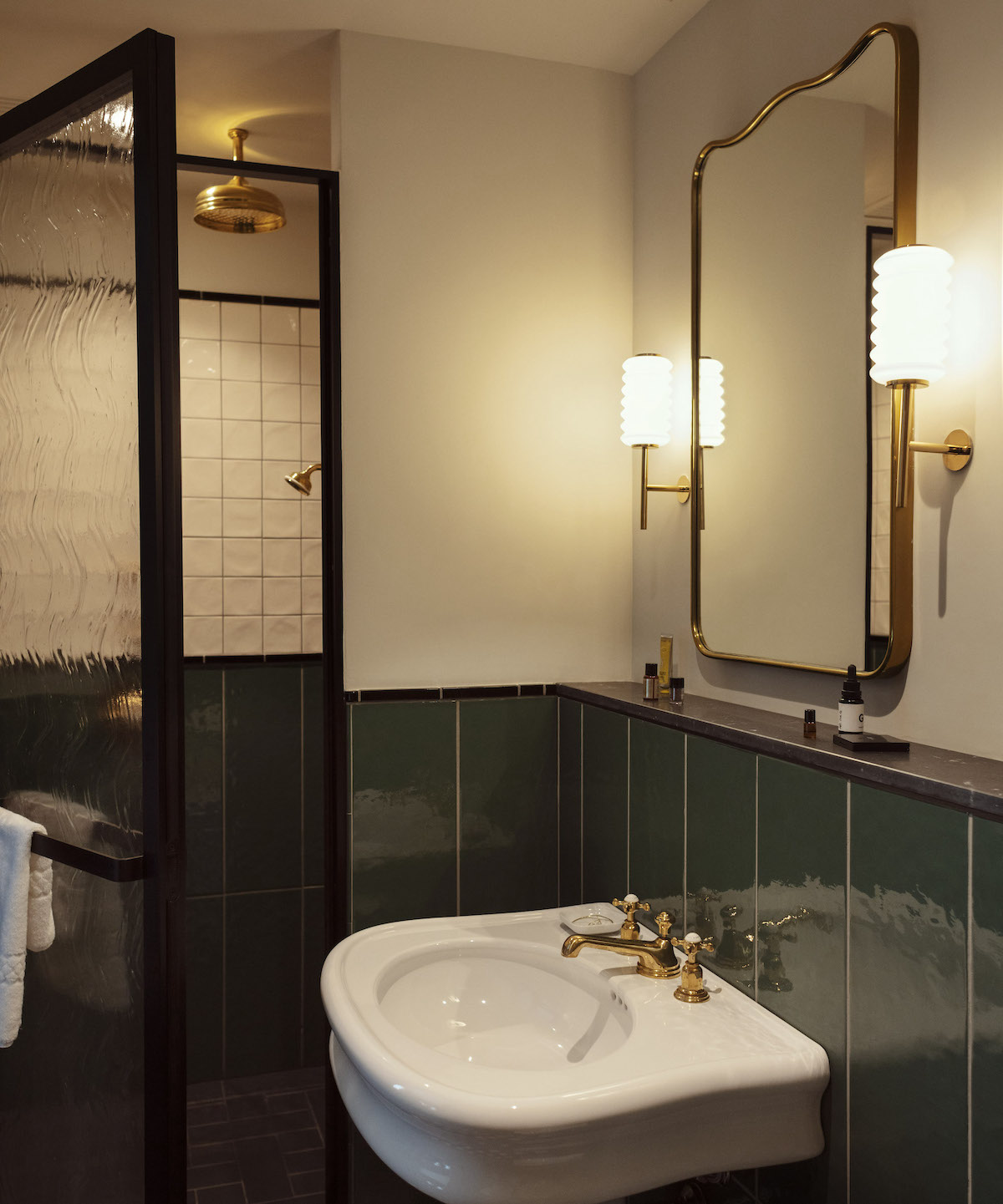
Image credit: Hoxton / Ennismore
As the sand inside the mold starts to crumble away, the skeleton of the product is revealed, but that is just the beginning of an extensive process that includes soldering, cutting, plating, polishing and quality care before this tap is ready for assembly.
For designers and architects to fully understand the journey of a Perrin & Rowe tap – and how the brand manufactures all 30-plus components for each product – House of Rohl is about to launch its first RIBA-approved CPD course, which will take its delegates through the production line. Like all new courses, lab-rat journalists are required to polish out the details, which is why I am spending the day in the region of England affectionately known as the Black Country, to appreciate, in person, a lack of mass production.
The Perrin & Rowe manufacturing process is almost hypnotising. It’s a well-oiled machine that is, almost single-handedly, keeping British bathroom manufacturing alive. I say ‘almost’ because, whatever way you look at it, skills such as casting, soldering and polishing – to the level required by Perrin & Rowe – are dying trades.
It’s no surprise, therefore, that at the heart of the factory are talented and interesting people. The team feel like a family, and in some cases they are. There are brothers working alongside sisters, uncles training nephews. Peter, for example, who’s brother and son also work on the factory floor, is a caster who has been with the company for 25 years.
In that time, little has changed in terms of the manufacturing process. Some tech has been introduced to allow the brand to achieve beyond-human accuracy when it comes to cutting threads in the pipes, for example, but much of the process has to remain handmade in order for the brand to maintain its high-quality reputation in a congested bathroom arena.
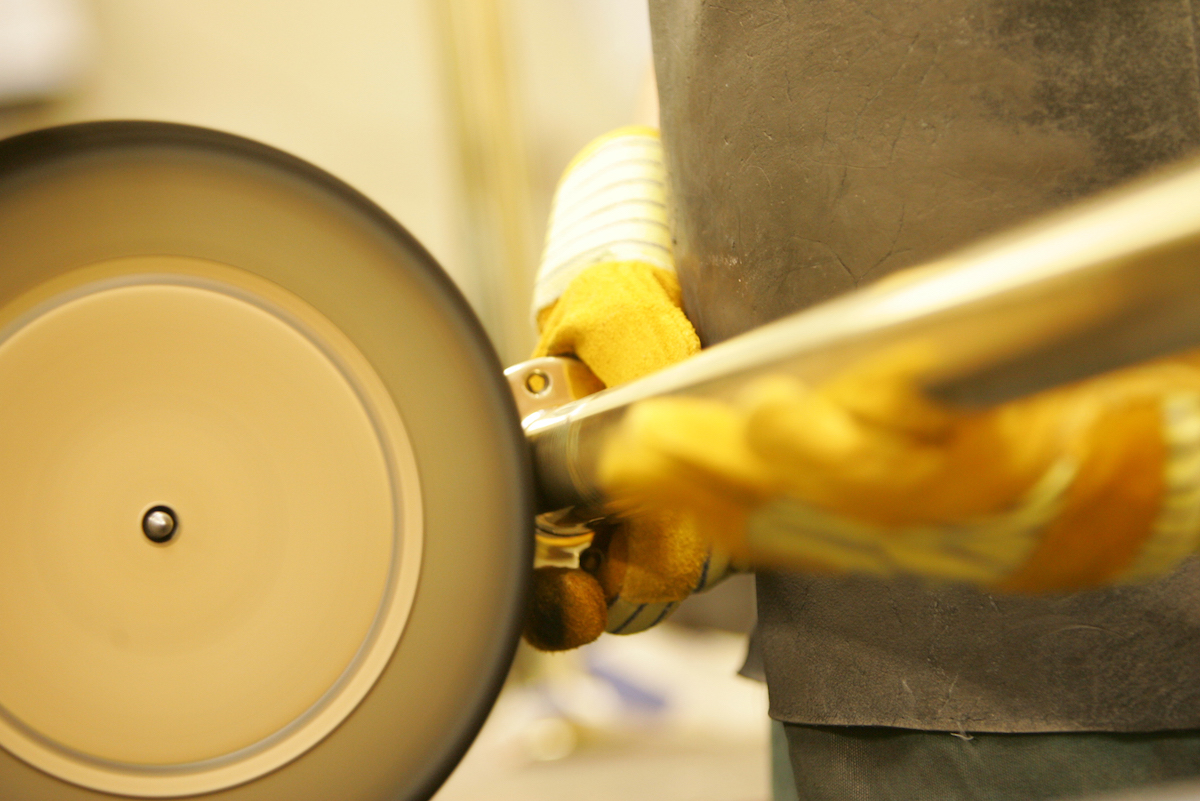
Image credit: Perrin & Rowe
Once each component is finished and soldered by hand, and after the plating stages, the most time-consuming – arguably most dangerous – part of the process takes place. Polishing can last hours to guarantee the Perrin & Rowe quality finish. This is where the brand also able to amplify its creative edge, with an extensive range of finishes that designers can choose from, including satin and aged-brass.
What I believe sets brands like Perrin & Rowe and groups like House of Rohl apart, aside from socially driving British manufacturing into a new era, are the intuitive environmental initiatives. Firstly, any offcuts are re-melted down and put back into the manufacturing process. And that’s not all. The group has a programme to recycle and reuse swarf and oil and House of Rohl has partnered with Severn Trent to process and safely discharge water.
The final part of the process, before the products are packaged and delivered to the brand’s other factory in Rainham, Essex, for final assembly, is the quality and water testing.
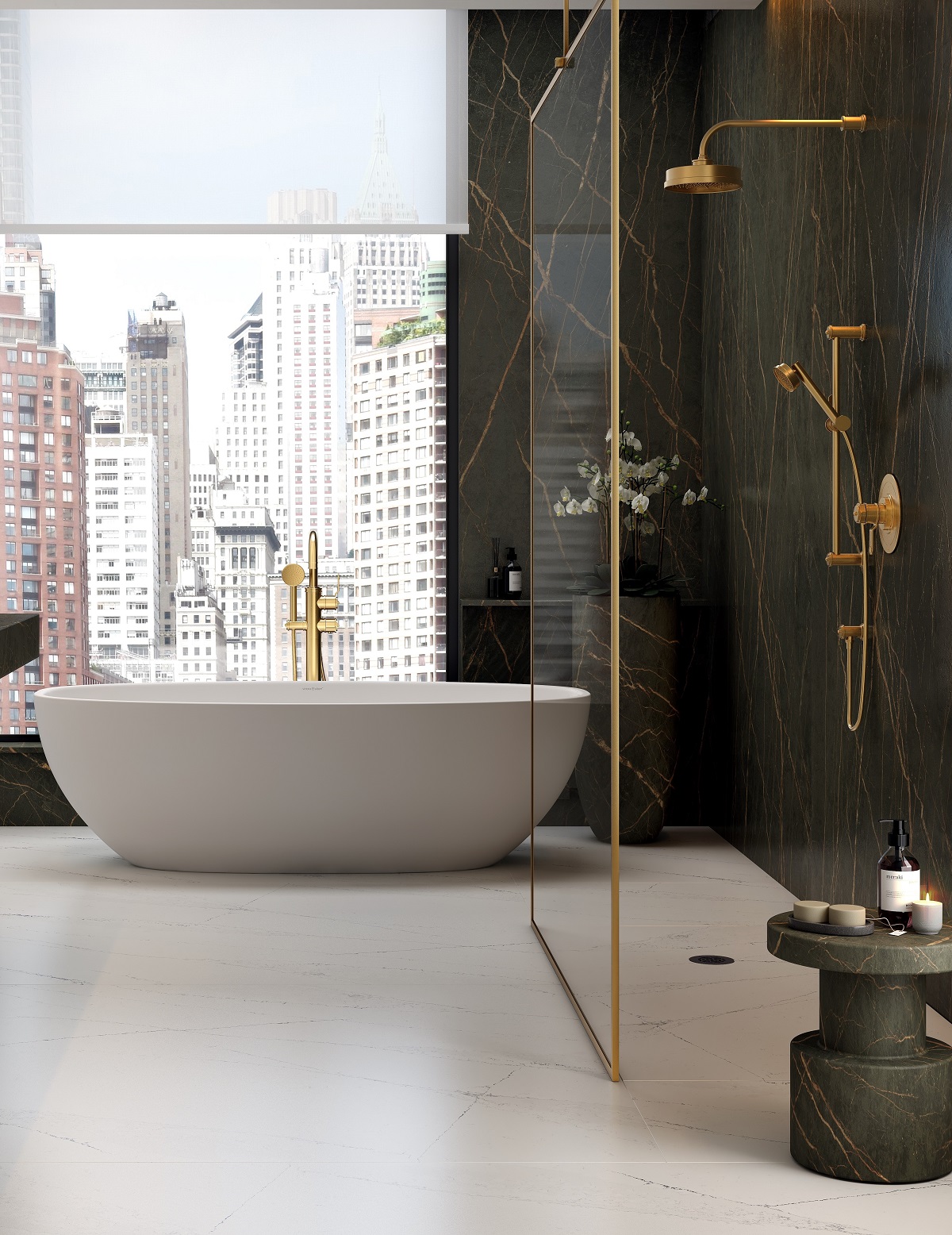
Image credit: Perrin & Rowe
So what gives this CPD course value and meaning? Well, put bluntly, it’s not like Perrin & Rowe needs the PR in order to get designers interested in its products. The fact that the brand is specified internationally in renowned hotels globally is an accurate measurement of the its success. Yes, by allowing designers in to discover the hands-on manufacturing process as it happens is an authentic way to allow designers to fully appreciate the various hands-on skills required to deliver the quality and quantity of products. But more than that, the CPD course will capture the design community to experience what put British manufacturing on the map in the first place – the brands who are not fuelled just by profit, but also by people. Perhaps, therefore, it is CDP with a dose of industry CPR to pump oxygen – and awareness – into the muscles of British manufacturing to keep it alive and healthy.
> Since you’re here, why not read about Perrin & Rowe’s new industrial-luxe bathroom collection?
House of Rohl is one of our Recommended Suppliers and regularly features in our Supplier News section of the website. If you are interested in becoming one of our Recommended Suppliers, please email Katy Phillips.
Main image credit: Perrin & Rowe