Michael Mulhall is Director of Sales at bespoke lighting specialist Dernier & Hamlyn where he leads on strategic direction and business development, while overseeing the company’s growing engineering, design and manufacturing facilities ensuring that they work together to meet clients’ exacting requirements…
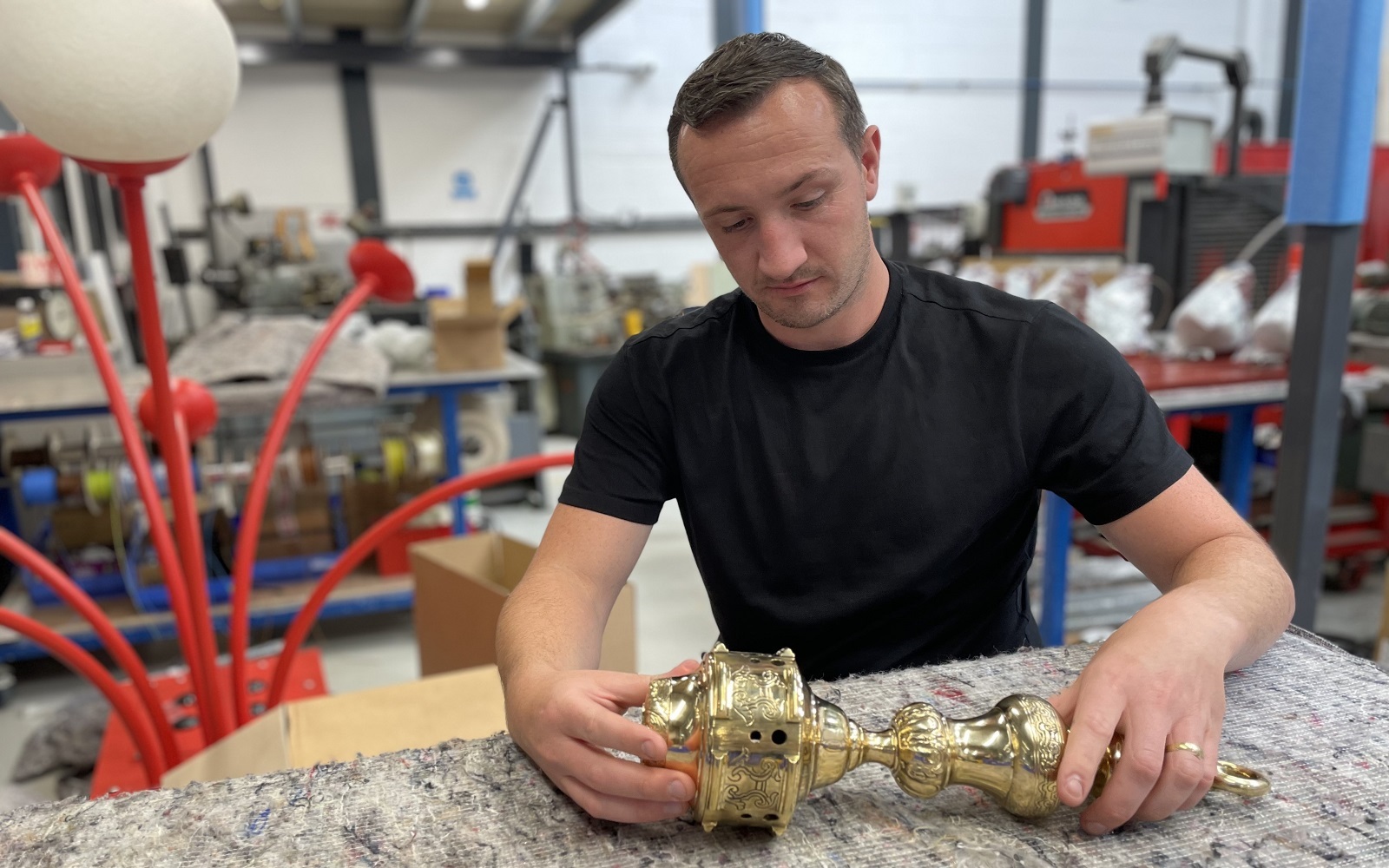
Dernier & Hamlyn is one of the few companies that designs and manufactures its fittings in the UK. Its factory in London is home to a team of specialist designers and artisans who produce pendants, chandeliers and other lighting individually made to meet designers’ specific requirements for luxury residences and hotels, superyachts and restaurants. With a rich history in the industry stretching back to 1888, the company is proud of its heritage and the unique experience and expertise the team has built up over the years, but the focus remains firmly on the future, with new techniques and materials being used alongside the traditional to produce beautiful custom-made lighting to meet designers’ requirements on time and on budget.
Hotel Designs sat down with Michael Mulhall to find out what is going on behind the scenes and on the workbenches in the Dernier & Hamlyn factory.
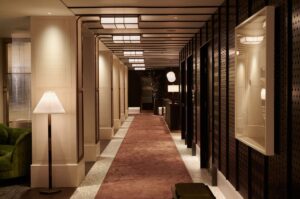
Image credit: Dernier & Hamlyn
Hotel Designs: What does Dernier & Hamlyn do?
Michael Mulhall: We design, make, refurbish, restore and install bespoke lighting for luxury homes, hotels, restaurants, superyachts and heritage buildings.
HD: What has changed for the company post pandemic?
MM: In terms of what we do day to day very little. We were working almost throughout because you can’t manufacture physical products by hand remotely. We do have more meetings with designers, suppliers and others remotely now, which certainly cuts down travel time. But there really is nothing like seeing the beautifully designed products our team turn into reality take shape from on screen images and printed engineering drawings to installation in their intended destinations using a whole host of traditional and very modern techniques and technologies.
HD: What’s in your factory currently?
MM: As ever it’s an eclectic mix. We have some chandeliers our team made around 40 years ago that are having their wiring updated and some broken elements repaired before they go back to a beautiful, listed building. Our studio team are working on some renders of lighting for reproduction art deco pendants and wall lights for a new hotel. And there is an awful lot of soldering and welding going on for a restaurant’s task lighting for their bedrooms and meeting rooms.
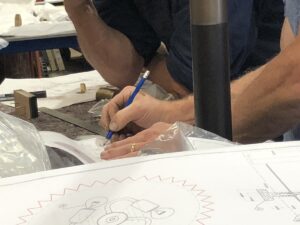
Image credit: Dernier & Hamlyn
HD: What keeps you awake at night?
MM: Not too much I’m glad to say. We have a business that’s almost unique in the UK and certainly none with our 135-year history and breadth of clients. We have a highly skilled, very experienced team that knows our business inside out, as well as some new people who have brought new and different experience and perspectives which is great too.
HD: What are you focussing on from a business perspective?
MM: We are quite a way down the route of venturing into complementary areas of lighting that is bringing challenges but also different opportunities which is very exciting. And, like many others, we are striving to be more sustainable and environmentally friendly. This makes moral and business sense, but also the more we can help our clients with their aspirations in this area the better. For example, where it makes economic and aesthetic sense, we encourage them to repurpose existing lighting rather than throw it away and manufacture from new. There has been a big shift on reusing materials and products differently. So that where it used to be seen as something you would only do if you absolutely had to, increasingly it’s designers preferred choice. If you can take existing bespoke lighting fittings and update them with, for example, new elements, different materials, alternative lamping options or hanging them in a more contemporary way you contribute to the design narrative by referencing a place’s past while acknowledging its future stories and it’s true circular economy stuff.
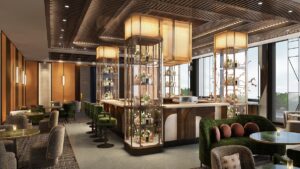
Image credit: Dernier & Hamlyn
QUICK-FIRE ROUND
HD: What is the best lighting project you have worked on and why?
MM: Nobu London Portman Square was one of the first hotel’s I worked on when I joined Dernier & Hamlyn and it was a fantastic project to be involved in. It was complicated, but as ever, our team stepped up to the mark and helped David Collins Studio achieve the ambience they wanted with more than 100 bespoke light fittings that are in various public areas of the hotel.
HD: What is your favourite part of the bespoke lighting process?
MM: I love it when designers come to us with an idea in their heads and we take them through from committing it to paper then to a digital format and into our factory and finally seeing it in its final destination where it was meant to be.
HD: What is your ideal client like?
MM: Clear on their vision, responsive to our ideas even if they don’t agree with them all, curious to push boundaries in the process but not beyond the realms of reality and happy to be part of the process rather than just a spectator. Oh and pay their invoices on time of course!
HD: Dernier & Hamlyn has always been based in and around London but you aren’t why’s that?
MM: I love visiting London but I love my family and friends more and I also love going on country walks and perhaps finishing in a village pub for a bit of lunch and a drink. I’m a country boy at heart!
Dernier & Hamlyn is one of our Recommended Suppliers and regularly features in our Supplier News section of the website. If you are interested in becoming one of our Recommended Suppliers, please email Katy Phillips.
Main image credit: Dernier & Hamlyn